|
 |
|
|
About SPF:
Boosting high performance, efficiency, and durability as well as low maintenance and cost of ownership, it's no surprise that Spray Polyurethane Foam has been used in the United States for over 30 years. Owners, Regulatory Authorities, Technical Groups, Contractors and even Environmental Groups alike praise it for it's broad range of benefits. This ultra-light space-age miracle material acts as unique and highly effective air barrier as well as offering an unparalleled level of thermal insulation to provide a more comfortable and energy efficient environment for you, your employees or family.
It can be applied to almost anything with minimal fuss. It's nearly indestructible. It's better then any other alternative construction method currently available.
Spray Polyurethane is composed of two chemicals called “Isocyanate” and the “Polyol Resin”. These basic compounds can be used for many different industries through equally varied application methods, but the system we'll be discussing is the Spray Polyurethane Foam for method used for Roofing and Insulation. In order to do this, several pieces of special trade equipment are employed as applicators. To begin, the individual barrels must be safely tapped and be prepared to feed into carrier hoses. The separate Isocyanate and Polyol Resin are then mixed in proper proportion as they are heated to high temperatures and, quite literally, are sprayed onto the target surface area. |
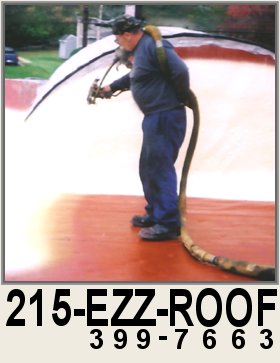 |
|
|
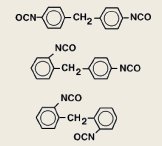 |
Isocyanate Molecules:
Methylene-Diphenyl-Diisocyanate |
|
Initially, the super-heated compound retains its liquid form for a short time after it is sprayed from the nozzle system onto the applied area. This allows the foam to penetrate places that other construction methods would miss so that costly gaps in the insulation are a thing of the past. As soon as it is applied to the surface, the mixture of Isocyanate and Polyol Resin will begin the process of molecular-level bonding and to create Polyurethane Foam. The exact process of the reaction varies by chemical component type, as do the specific properties of the resultant material. The system self-seals and flashes allowing it to conform to irregular shapes, sizes, and textures with no need for fasteners that are notoriously forms of Thermal Bridging. And, thanks to the simplicity of gravity, the liquid compound will apply to the surface area at a very level rate that will significantly reduce the risk of potentially dangerous water and ice pools on roofing. |
As a fully self-adhesive plastic, the material will successfully bind not only with itself, but nearly any surface material it contacts with. During the creation process of the final chemical compound, polyfunctional polyols are create a three-dimensional cross-linked matrix of molecules. Cyclic structures then form within the matrix lending a further rigidity, or hardness, along with more thermal stability. A bonus to this process is that the a roof not only gains an excellent Wind Resistance rating due to the molecular bonding, but also aids the building in becoming more durable to resistance against thermal expansion and contraction.
Simultaneously, due to the heat at which the Spray Polyurethane Foam is delivered another chemical reaction is taking place. The liquid state Polyurethane steams, bubbles and expands into a froth that is 20-30 times the volume of it's original size, and begins to rapidly harden into a solid-state. As it does so, natural gasses such as oxygen, hydrogen, nitrogen, and carbon dioxide that are created as a result of the chemical reactions become trapped within the rigid Polyurethane cell. Such trapped gas within the cell makes thermal interaction between layers very difficult, creating an unsurpassed insulation rating along |
with an excellent barrier to water and condensation.
Within seconds of being applied, the process of Spray Polyurethane Foaming is completed, though the roofing process isn't yet complete. After the Polyurethane is fully dried and set a coating is applied to the roof to protect it from one harmful aspect that can, over time, damage the Foam: corrosion due to sun exposure. The method of such coating varies by building type, construction capacity, and client material requests, however the most commonly used coatings are Acrylic, Earth, or (rarely) Metal coatings.
|
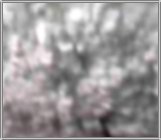 |
Close up of Polyurethane Foam immediately after spraying. |
|
|
|
 |
|
 |
|
|
|
|
|
|
|
|
|
|